Actual examples of Restoration Work.
We introduce three examples.
1) A Wakizashi, polish, habaki, and shirasaya.
2) A Wakizashi, polish, habaki, and
producing new koshirae.
3) A Wakizashi, getting a poor result.
1) A Wakizashi, polish, habaki, and shirasaya.
A rusted blade
blade length 52.1cm, width at the base 2.9cm,
thickness 7mm
This is an original mumei wakizashi from Shinto period.
It is healthy with neat shape, and attractive with the active patterned
hamon. But there is one open layer. If you don't mind such a small fault,
this blade should get its beauty again. The old scabbard is very destroyed. There is no habaki.
It is polished up with the classical style (Sashikomi style). It has turned
far better than we thought before polishing. The hamon is bright and there
are many attractive appearances that come from the relation between the
steel and the tempering. The polisher said the steel in the hamon is good.
The steel has a visible wood grain layer pattern. The layer makes many
appearances into the hamon. The layer looks rough, but the steel quality is not bad.
The brightness of hamon means it.

The hamon is a Gunome pattern made of Nie (large particles).
The temper line is bright, having gradation of Nie into the hamon, and
it makes tapered Ashi with sweeping pattern.
The hamon in kissaki is a round pattern made of much
Nie with sweeping pattern. The Nie particles flow up into Ji. The turn
back is long.
The period is Edo (17th - 19th century).
Copper habaki
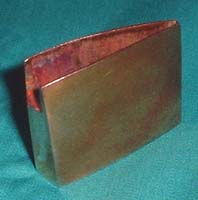
Sketch of hamon (Oshigata)
This is a case of success. Don't think that all the destroyed
swords can be getting good by restoration work. Condition and Quality of
the blade is important to consider restoration work. Sometimes the result
is poor than our expecting. That means a little gamble.
2) A Wakizashi, polish, habaki, and
producing new koshirae.
A rusted blade
blade length 54.1cm, thickness at the base 7mm,
width at the base 3.0cm
The part polishing.
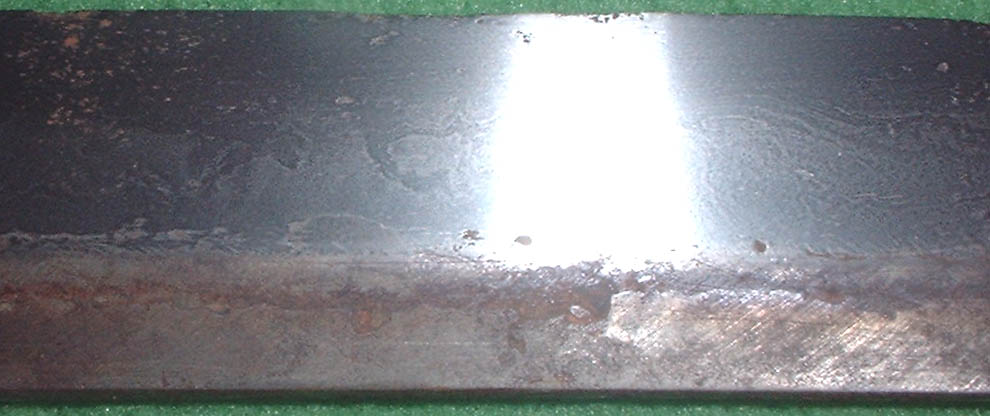
The part where the rust is deepest.
The foundation work for shaping is done.

blade length 54.1cm, thickness at the base 7mm, width
at the base 2.7cm
The obverse side becomes very clean.
On the reverse side, several small dimples are left and
some rough layer appears.
The silver habaki is finished.
made by Mr. Shizuo SUGAWARA
Fittings for koshirae are prepared.
The fuchi/kashira and the tsuba.
The blade in the midway of shaping work and the fittings
are brought to the scabbard maker.
The base of mount made by Mr. Yoshio NAKAJIMA.
The scabbard goes to lacquer work, and the handle goes
to ray skin wrapping.
The lacquer work by Mr. Ken'ichi SAKUMA
The blade within the scabbard go to the polisher again
to finish the polishing work.
The polishing work is finished. It is the modern style (Hadori style).
The blade has much appearances in the whole of surface. It is very attractive
that the layer pattern and the nie particles run actively. It suggests
Soshu tradition in Koto period.
The blade has recalled completely clean surface on the
obverse side, but several pitiful dimples are left on the reverse side.
The dimples are filled with urushi lacquer to prevent rusting.

Polished by Mr. Akio MURAKI
Steel
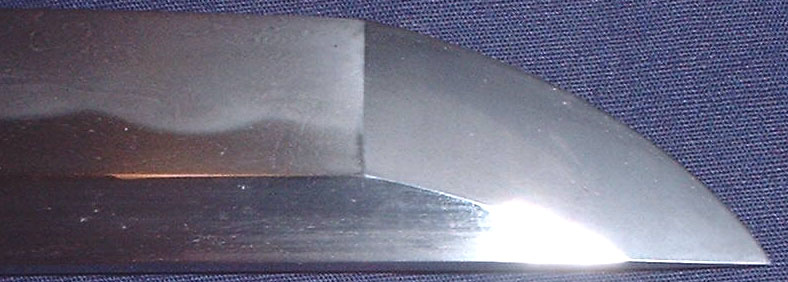
Hamon
The kogai hole of the tsuba is filled with gold. The work is done by Mr.
Shizuo SUGAWARA.
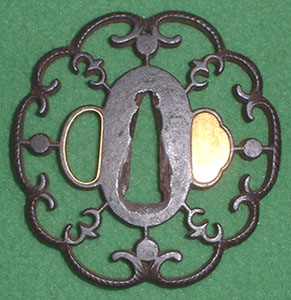
The handle has been wrapped with ray skin and hardened
with urushi lacquer.
When the blade is returned from the polisher, the mekugi
and the other fittings are confirmed and fixed again, then the tsuka is
wrapped with silk cord.
The menuki.
It is very matching to the fuchi.

The handle is completed.
Put the silk cord on the scabbard and the bag.
These works have taken about one year, from the rust
blade to the completion of the koshirae.
3) A Wakizashi, getting a poor result.
A naked Shin-shinto wakizashi covered with rust, but
the rust is not very deep. There is a famous smith's signature on the tang.
The hamachi is broken, so it must be fixed to make habaki.
On the stage of Chu-nagura stone, the blade is brought
to habaki worker to make new one.

The blade with new habaki is brought to shirasaya making,
then brought back to the polisher again.
On the stage of Koma-nagura stone, a crack appears in the hamon. Then we
stop the work, since there is no point to continue the work. It is just
a wasting of money.
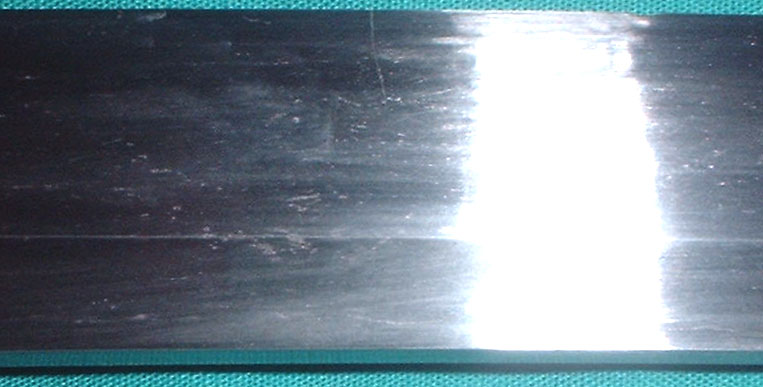
Home > Information > Restoration